The Science Behind Porosity: A Comprehensive Guide for Welders and Fabricators
Understanding the elaborate mechanisms behind porosity in welding is crucial for welders and fabricators pursuing impeccable craftsmanship. As metalworkers look into the midsts of this sensation, they discover a world governed by different aspects that affect the development of these small voids within welds. From the make-up of the base products to the details of the welding process itself, a wide range of variables conspire to either aggravate or relieve the visibility of porosity. In this thorough overview, we will certainly unravel the science behind porosity, exploring its impacts on weld high quality and unveiling progressed strategies for its control. Join us on this trip with the microcosm of welding blemishes, where accuracy satisfies understanding in the quest of remarkable welds.
Understanding Porosity in Welding
FIRST SENTENCE:
Examination of porosity in welding exposes essential understandings right into the stability and quality of the weld joint. Porosity, defined by the presence of cavities or gaps within the weld metal, is a common problem in welding procedures. These spaces, otherwise effectively attended to, can endanger the structural honesty and mechanical properties of the weld, causing potential failings in the ended up product.
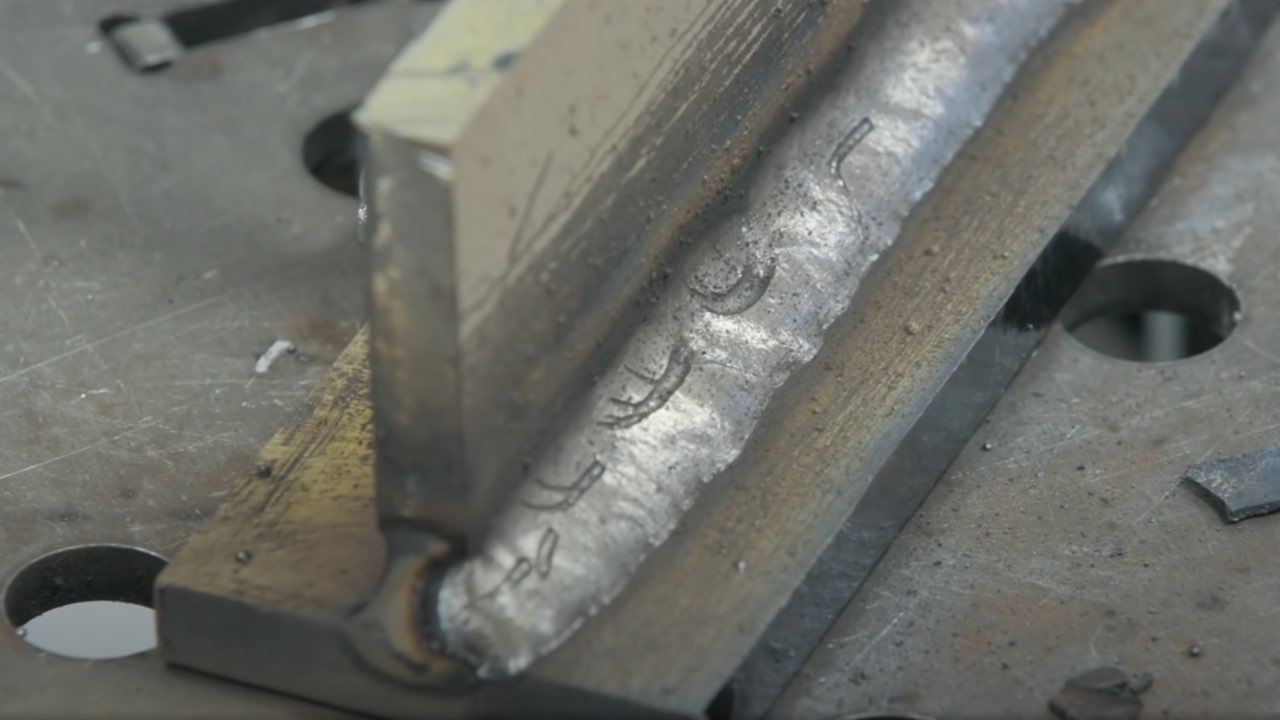
To spot and evaluate porosity, non-destructive screening techniques such as ultrasonic testing or X-ray examination are usually employed. These techniques permit the identification of inner flaws without jeopardizing the stability of the weld. By evaluating the dimension, form, and distribution of porosity within a weld, welders can make enlightened decisions to boost their welding processes and accomplish sounder weld joints.

Factors Influencing Porosity Formation
The incident of porosity in welding is affected by a myriad of variables, ranging from gas securing efficiency to the details of welding parameter settings. One essential variable adding to porosity formation is insufficient gas securing. When the securing gas, commonly argon or carbon dioxide, is not efficiently covering the weld pool, atmospheric gases like oxygen and nitrogen can contaminate the liquified metal, leading to porosity. In addition, the cleanliness of the base products plays a substantial role. Impurities such as rust, oil, or moisture can vaporize throughout welding, developing gas pockets within the weld. Welding specifications, including voltage, present, take a trip speed, and electrode type, additionally effect porosity development. Using inappropriate settings can produce extreme spatter or warmth input, which subsequently can result in porosity. In addition, the welding technique used, such as gas steel arc welding (GMAW) or protected metal arc welding (SMAW), can affect porosity formation due to variations in warm circulation and gas insurance coverage. Comprehending and managing these aspects are crucial for lessening porosity in welding operations.
Impacts of Porosity on Weld Top Quality
Porosity formation substantially jeopardizes the architectural honesty and mechanical properties of welded joints. When porosity is present in a weld, it creates voids or dental caries within the product, decreasing the total toughness of the joint. These gaps act as stress and anxiety concentration points, making the weld more prone to cracking and failing under load. The presence of porosity likewise compromises the weld's resistance to deterioration, as the entraped air or gases within deep spaces can react with the surrounding atmosphere, resulting in destruction in time. In addition, porosity can prevent the weld's ability to stand up to stress or impact, additional threatening the total quality and integrity of the welded structure. In essential applications such as aerospace, auto, or structural building and constructions, where safety and security and longevity are critical, the detrimental effects of porosity on weld quality can have extreme effects, stressing the importance of reducing porosity through appropriate welding methods and treatments.
Strategies to Minimize Porosity
To improve the top quality of bonded joints and make certain architectural stability, welders and producers employ details strategies aimed at decreasing the development of gaps and dental caries within the product throughout the welding procedure. One effective method to reduce porosity is to ensure appropriate product prep work. This consists of complete cleaning of the base metal to eliminate any type of contaminants such as oil, oil, or dampness that can add to porosity formation. Furthermore, making use of the ideal welding specifications, such as the right voltage, present, and take a trip speed, is crucial in preventing porosity. Maintaining a constant arc length and angle throughout welding additionally helps in reducing the possibility of porosity.

Additionally, selecting the appropriate shielding gas and keeping appropriate gas flow rates are crucial in decreasing porosity. Using the appropriate welding technique, such as back-stepping or utilizing a weaving movement, can also help distribute warmth equally and lower the opportunities of porosity development. Last but not least, ensuring appropriate air flow in the welding setting to get rid of why not try here any kind of possible resources of contamination is crucial for accomplishing porosity-free welds. By implementing these techniques, welders can successfully reduce porosity and create top notch bonded joints.
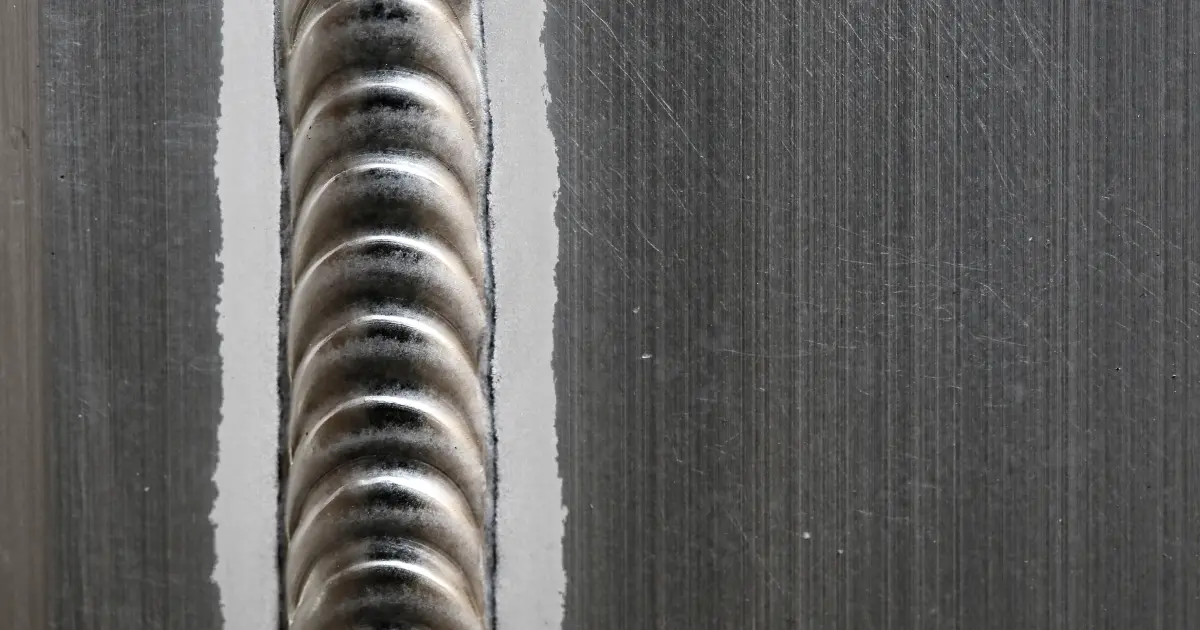
Advanced Solutions for Porosity Control
Applying innovative innovations and cutting-edge methods plays a pivotal function in attaining superior control over porosity in welding procedures. Furthermore, employing innovative welding strategies such as pulsed MIG welding or changed environment welding can also assist minimize porosity issues.
Another innovative option entails using innovative welding equipment. For circumstances, utilizing devices with integrated features like waveform control and innovative source of power can improve weld top quality and lower porosity risks. In addition, the implementation of automated welding systems with specific control over specifications can considerably reduce porosity issues.
Furthermore, including innovative monitoring and inspection technologies such as real-time X-ray imaging or automated ultrasonic testing can help in spotting porosity early in the welding procedure, enabling immediate rehabilitative activities. Generally, integrating these advanced solutions can significantly enhance porosity control and improve the total quality of bonded parts.
Verdict
To conclude, recognizing the scientific research behind porosity in welding click here to find out more is important for welders and producers to create premium welds. By identifying the elements affecting porosity development and implementing strategies to minimize it, welders can improve the overall weld high quality. Advanced solutions for porosity control can better improve the welding process and make sure a solid and reputable weld. It is necessary for welders to continuously inform themselves on porosity click here for info and carry out finest methods to achieve optimal outcomes.